Rohbau der Schalttafel
Jetzt geht es in die Produktion …
Im vorherigen Kapitel haben wir den Prototypen gebaut, mit dem neben der theoretischen Planung weitere Erkenntnisse zur Schalttafel gewonnen wurden. Nach der Realisierung dieser Urform soll jetzt das Produkt „in Serie“ gebaut werden. Das Vorgehen ist wie folgt:
- Die in den vorherigen Kapitel erstellte fertige 1:1 Sägeschablone wird ausgedruckt und ausgeschnitten.
- Diese ausgeschnittene Sägeschablone überträgt man sodann auf ein geeignetes Stück Holz. Geeignet für die Gehäuse-Seiten sind z.B. Sperrholz, Spanplatte oder MDF. Die Mindestdicke sollte 8-10mm nicht unterschreiten (siehe folgendes Bild).
- Ausschneiden der ersten Seitenwand mit einem geeigneten Werkzeug. Dies ist entweder eine Stichsäge, eine Dekupiersäge oder – für Sperrholz – auch eine manuelle Säge.
- manuelle Nachbearbeitung des Zuschnitts mit einer Feile und / oder mit Schleifpapier bis schliesslich die Ur-Form der Seitenwand fertig ist.
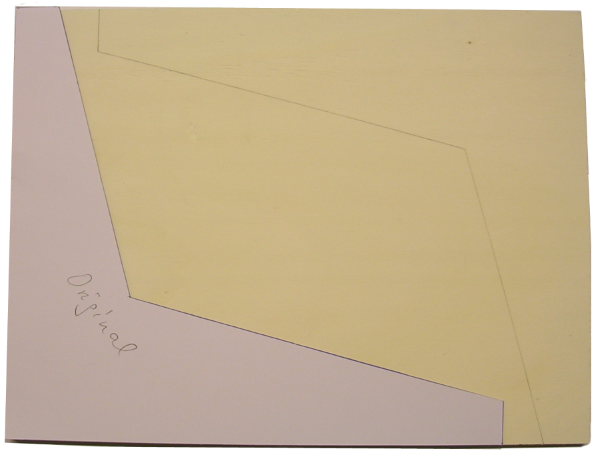
Mit dieser Urform der Gehäuse-Wand können alle benötigten, gleichen Wandelemente gebaut werden. Die Urform wird einfach immer wieder auf das gewählte Holz aufgezeichnet und ausgesägt. Der Vorgang wird demnach sooft wiederholt, bis alle Wände hergestellt sind.
Tipp: die Urform wird nicht für den Bau der Schalttafel verwendet, sondern gut aufgehoben, damit sie für eine spätere Erweiterung des Schaltpults zur Verfügung steht.
Die zugeschnittenen Wände werden im nächsten Schritt auf genau gleiche Abmessungen überprüft. Sollten sich noch Abweichungen ergeben, kann mit einer oder mehreren Feilen nachgeholfen werden. Zuletzt werden alle Kanten geschliffen, damit sie glatt werden. Das Resultat zeigt das Bild:
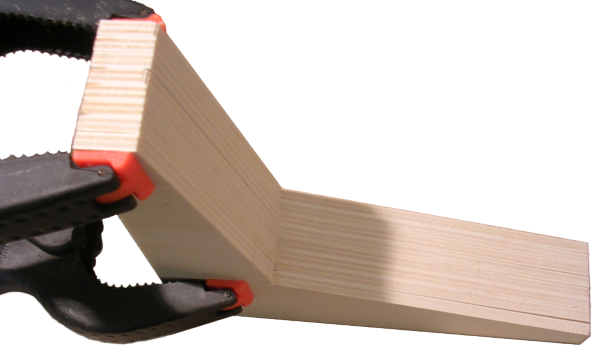
Tipp: Je sorgfältiger man hier arbeitet, desto gleichmässiger wird nachher die Gehäuseform. Es lohnt sich also hier Zeit zu investieren.
Der nächste Schritt besteht darin, ein Segment der Schalttafel zusammenzubauen. Schaut man sich nochmals meinen Entwurf an, so wäre dieses Segment der ganz linke Teil der Schalttafel, der eine obere und eine untere Funktionselemente-Gruppe (Taster) aufnimmt.
Für diesen Teil fehlen noch ein paar Voraussetzungen:
- Die Breite dieses Segments muss bestimmt werden
- Die Holzleisten, die die Gehäusewände zusammenhalten, müssen hergestellt werden
- Es braucht eine Schablone zur Herstellung der Holzleisten. Diese muss gefertigt werden
- Zuletzt braucht es eine Schablone, für den Zusammenbau der Wänden mit den Leisten
Die Segementbreite bestimmt sich aus der Breite der Funktionselemente-Gruppe resp. aus den ausgewählten Tastern, mit denen ein Funktionsblock realisiert wird plus den benötigten Abständen zu den Rändern. Hier muss bedacht werden, dass die Taster nachher auch beschriftet werden sollten, daher noch genügend Platz gelassen wird.
Die Holzleisten, die Seitenwände schliesslich zusammenhalten, haben Länge von
Wenn also das Segment 6 cm breit sein soll, und für die Seitenwände z.B. Sperrholz mit 8 mm Dicke gewählt wurde, dann braucht es Holzleisten mit 4.4 cm Länge.
Zur Herstellung der Holzleisten braucht es eine Schablone, denn auch hier gilt, je genauer die Leisten zugesägt werden, desto besser das Gesamtresultat. Dabei kommt es auf 2 Dinge an: zum einen der exakten Länge der Leisten, zum anderen auf den genau rechtwinkligen Schnitt. Ein Blick auf die Schablone für die Holzleisten:
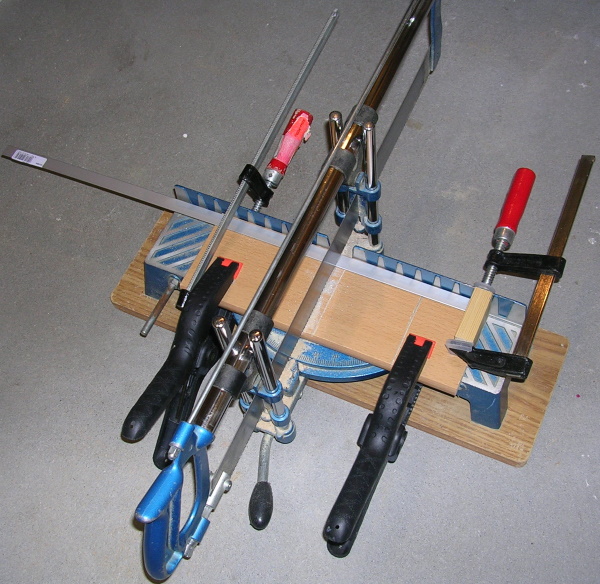
Wie auch für die Seitenwände gilt hier ebenso, dass möglichst alle gleichen Holzleisten in einem Rutsch zugesägt werden sollten. So ist gewährleistet, dass auch alle gleich lang sind.
Tipp: es macht Sinn, sich wenigstens eine Leiste auf Reserve zu sägen. So kann man später die Schablone wieder neu darauf justieren.
Übrigens zeigt das voranstehende Bild nicht die Sägeschablone für eine Holzleiste. Die Schablone war speziell für eine Aluleiste der Frontplatte. Dazu kommen wir später, das Prinzip ist jedoch das gleiche.
Tipp: die Holzleiste muss stark und breit genug gewählt werden, damit sie nachher die Seitenwände auch halten, sprich, es genügend Klebefläche gibt. Andererseits dürfen sie auch nicht im Weg stehen, und den Zugang zu den Funktionselementen versperren oder gar den Einbau dieser in die Frontplatte verhindern. Hier hilft immer wieder planen und messen.
Jetzt hat man neben den Seitenwänden auch alle Holzleisten für den Zusammenbau der einzelnen Schalttafel-Segmente fertig gestellt. Für diesen Zusammenbau ist es sehr wichtig, auf exakte Ausrichtung der Wände und auf rechte Winkel zu achten. Auch hier gilt, dass maximale Sorgfalt für ein perfektes Ergebnis notwendig ist. Und es braucht wieder eine Schablone.
Im folgenden Bild ist diese Schablone gezeigt. Es handelt sich dabei im wesentlichen um ein Holzbrett, auf das 2 Brettchen senkrecht aufgeklebt werden. Zwischen diesen Brettchen und am ebenfalls erkennbaren Anschlag werden alle gleichen Segmente der Schalttafel nach und nach endmontiert. Der Abstand der senkrechten Brettchen beträgt dabei exakt die Breite des Segments.
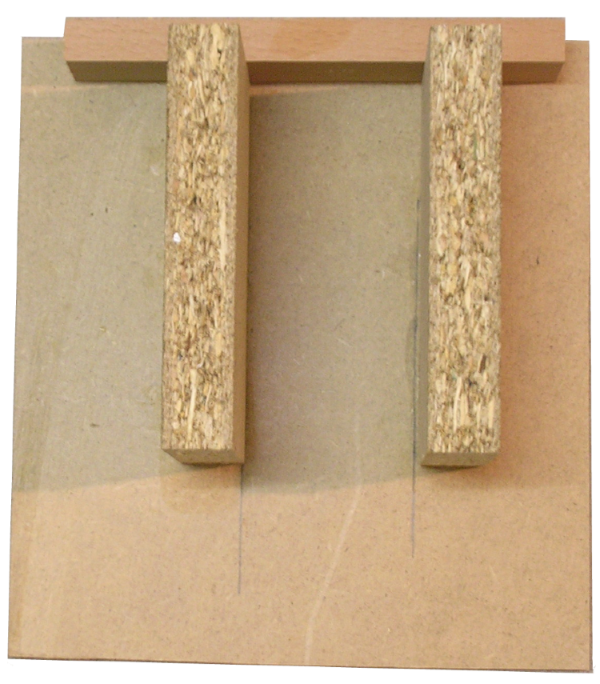
So erfolgt der Zusammenbau:
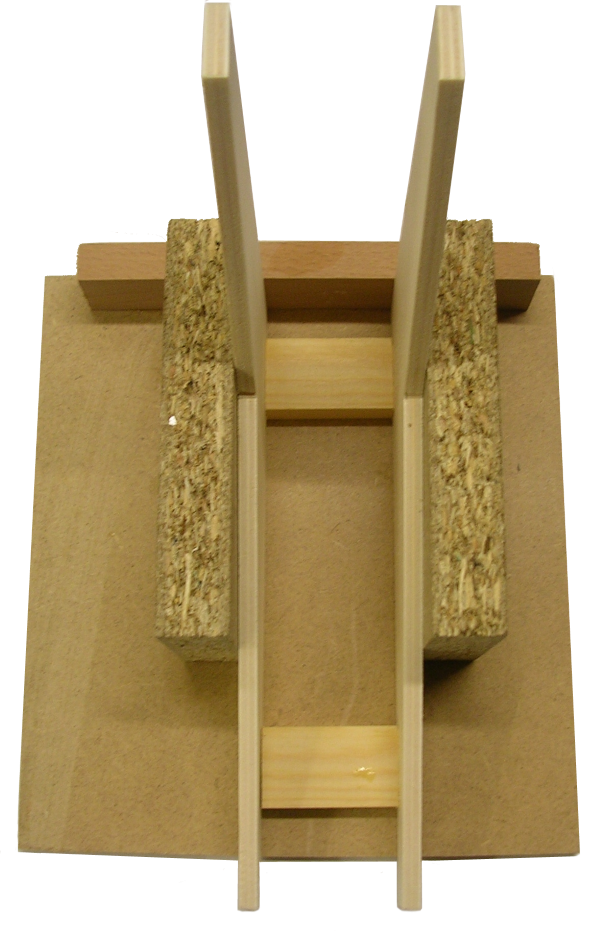
Deutlich ist im vorherigen Bild zu erkennen, wie die Seitenwände des Segments durch die seitlichen Brettchen und am oberen Führungssteg ausgerichtet werden. Es sind auch zwei von insgesamt drei Holzleisten erkennbar, die die Seitenwände zusammenhalten. Die Stirnseiten der Holzleisten wurden vorher mit Holzleim versehen.
Wenn jetzt alles sorgfältig vorbereitet wurde, dann sind die Seitenwände jetzt exakt parallel ausgerichtet und über die Holzleisten solide miteinander verklebt. Es fehlt noch die dritte Holzleiste, die das obere Ende des Schalttafel-Segments zusammenhält (ist später noch zu sehen). Damit ist der Rohbau für dieses Segment beendet, und alle gleichen Segmente können nach und nach hergestellt werden.